
6K Energy Technology
Introducing the Advantages of UniMelt by 6K
At the heart of 6K Energy is the unique, proprietary UniMelt process, the world’s first full-scale microwave plasma production system.
UniMelt microwave plasma platform provides:
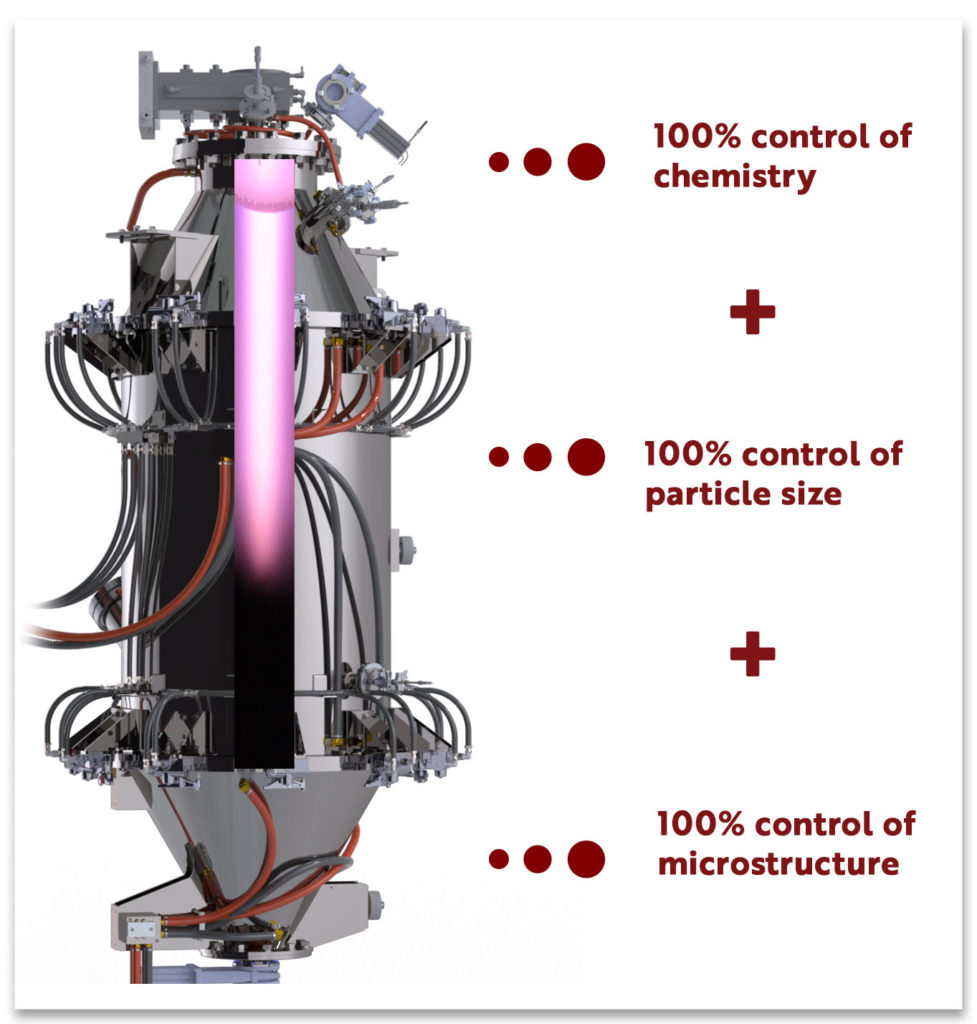
The UniMelt is well positioned to replace today’s traditional manufacturing processes, which are constrained by the limitations of conventional synthetic routes and processing methods. Traditional manufacturing methods for NMC cathode using coprecipitation can take 2-3 days, spanning multiple energy-intensive and waste-producing steps. 6K collapses the production time from days to as little as two seconds, drastically reducing the conversion costs and production Capex.
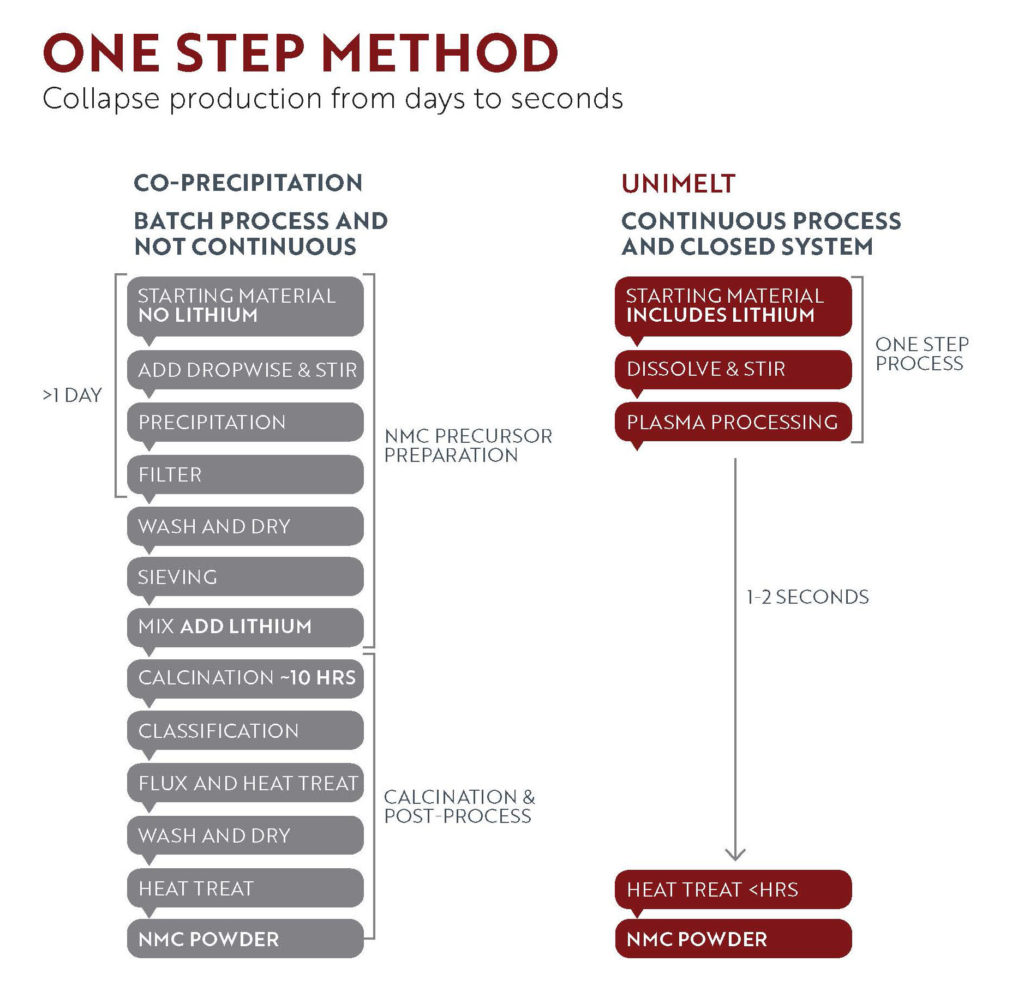
UniMelt Technology – a revolutionary sustainable manufacturing process
Not only does producing batteries use a wide range of raw materials, including metals and non-metals, but the battery industry can also generate considerable amounts of environmental pollutants (e.g., hazardous waste, greenhouse gas emissions, and toxic gases). The development of energy storage is increasingly being looked at as an indispensable component of sustainability. While it is clear that electric vehicles are far and away more sustainable than gas combustion vehicles, the manufacturing processes employed to produce the materials for the batteries used in EVs are not only dated, but environmentally unfriendly and counter to the mission of sustainability and rationale for EVs.
Lithium-ion batteries contain materials spanning the full spectrum, including ceramics, metals, polymers, lithium salts, carbon and graphite, and increasingly, silicon-based materials. While electrification of vehicles and the grid is a key component of a sustainable energy strategy, the manufacturing processes for many key battery materials are not well aligned with the environmental end goals. Traditional material manufacturing processes like coprecipitation (used in the production of NMC cathodes) generate large amounts of environmental pollutants, consume huge amounts of water, and use highly energy-intensive processes.
