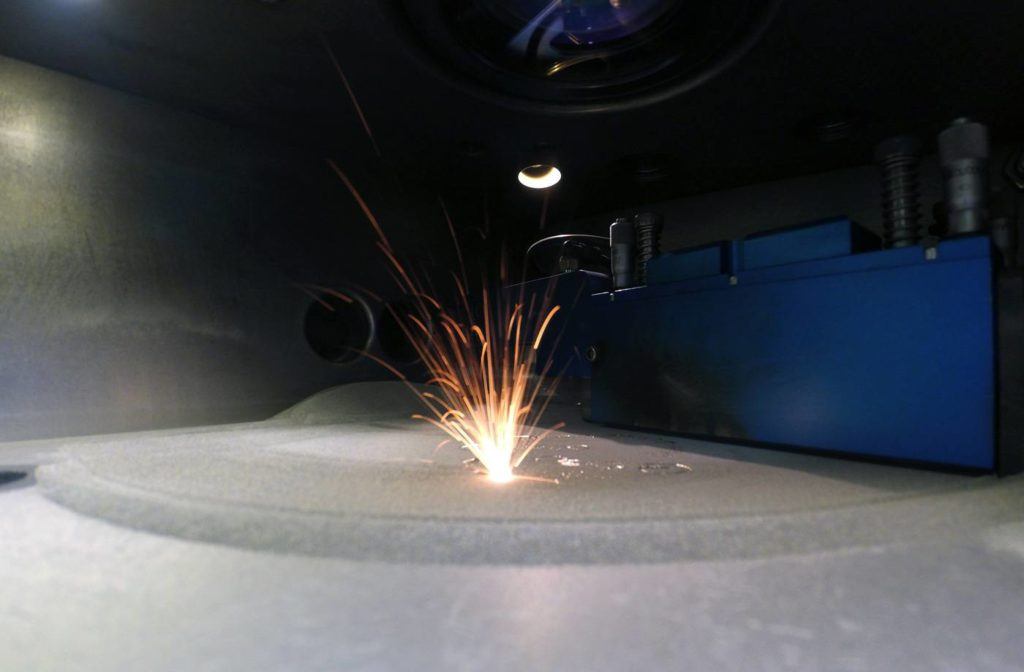
Additive Powders - L-PBF, EBM, Binder Jet, & DED
Spheroidization: The Ultimate Step For Additive Materials
6K’s UniMelt® spheroidization and densification process creates premium quality powders, avoiding the challenges and downstream costs of traditional atomization processes.
Spheroidization is the process of transforming angular and irregular shaped materials into dense, spherical and uniform powders without the altering of the stoichiometry of the alloy. 6K’s highly uniform microwave-based plasma ensures every particle undergoes the same thermal profile, enabling targeted partial melting and minimized alloy volatilization.
PSD “IN” equals PSD “OUT.” Plasma Spheroidization is a volume conservation process. The volume of particles going in plasma is the volume of the particles coming out of plasma. Due to this, 6K can tailor the PSD specific to AM process such as MIM, L-PBF, EBM, DED or Binder-jetting. 6K’s proprietary preprocessing route enables 100% yield withing targeted PSD.
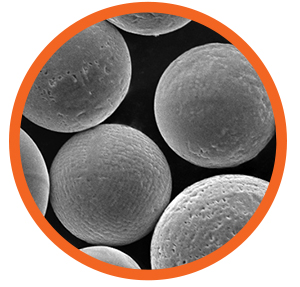
Premium Powders For Advance Applications
Medical, Aerospace, Automotive, Dental, and other AM applications demand diverse requirements. 6K’s UniMelt® technology can spheroidize ferrous alloys like SS17-4PH, SS316, nickel superalloys including Inconel 718, 625, HX, cobalt-base alloys like CoCr, refractory metals like Mo, W, Re, reactive alloys such as Ti-6-4, TiAl, Al alloys as well as high-temperature ceramics such as MY and YSZ.
Powders processed by UniMelt are highly spherical with no satellites, no internal porosity, high flowability, high tap density, and tailored particle size distribution. Unlike atomization processes, 6K’s UniMelt® process does not use high-velocity gases to disintegrate molten metal flow significantly reducing the risk of gas entrapment in the solidifying particles resulting in highly dense powder particles.
We provide our strategic partners with higher quality materials for demanding applications, and the opportunity to engage in new business models:
- Premium fresh powders from various raw material sources: HDH, water atomized and spray-dried powders.
- True recycling of used powders, eliminating satellites, eliminating organics and improving flowability and sphericity.
- Manufacturing next-generation engineered alloy spherical powders, not previously possible.
- Premium powders from high-value end of life components.
6K is working with strategic partners across markets and industries – specifically, those that are looking for high purity, spherical and low porosity powders.