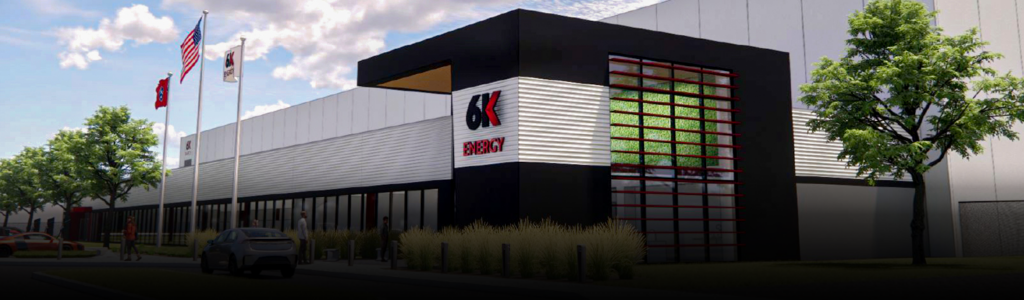
6K Energy - Battery Material Production Made in the USA
Processing Battery Material in Jackson, TN Supporting our Nation’s Energy Storage and AI Infrastructure
Highly Efficient Process – Transforming the Way Battery Material is Produced
Domestic battery material production at a fraction of the cost.
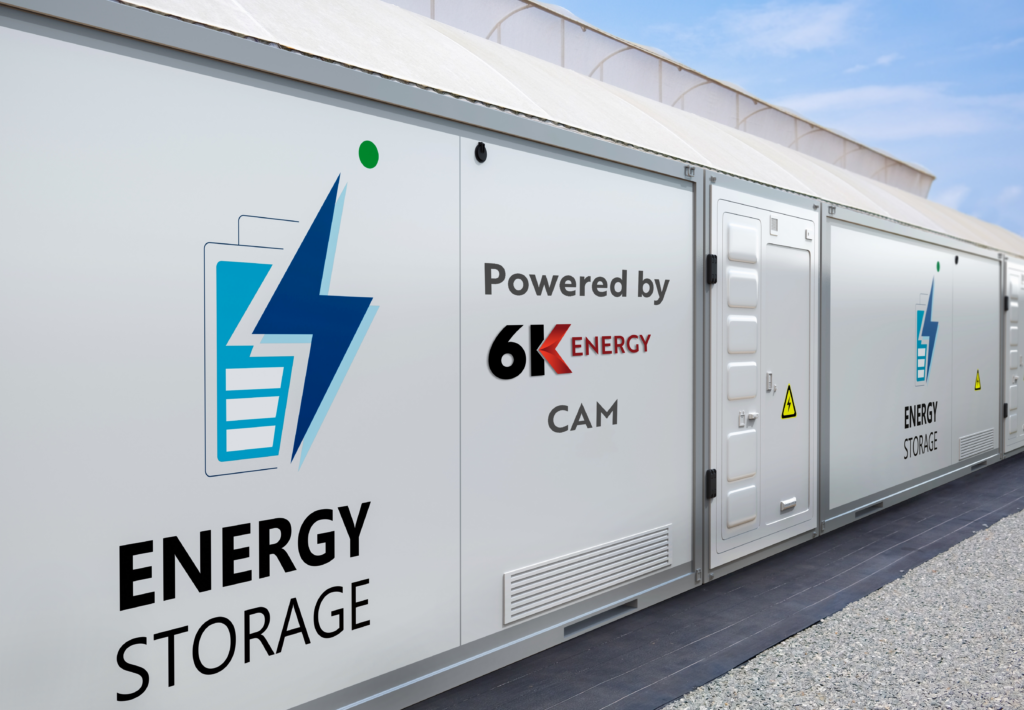
6K Energy – Powering our nation’s infrastructure
Innovative Battery Material Production
6K Energy’s UniMelt Technology Offers Unlimited Possibilities
6K Energy’s UniMelt technology can produce almost any lithium-ion battery material including NMC and LFP cathode active material. Market demand has expanded our material development to diversify our product portfolio to support ESS and critical infrastructure for higher cycle life and performance.
NMC Battery Material Properties
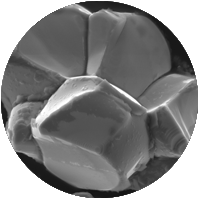
NMC (nickel, manganese, cobalt)
NMC batteries’ long-life cycles make them popular for critical energy storage systems, grid storage, AI framework as well as portable devices such as laptops and cell phones. Transportation mobility also use NMC battery material due to their high energy density and ability to withstand high discharge rates allowing longer distances on a single charge. The ratio of nickel, manganese and cobalt vary depending on applications.
LFP Battery Material Properties
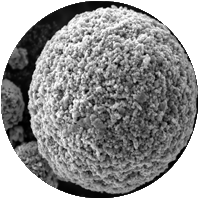
LFP (lithium iron phosphate)
LFP batteries outlast other types of batteries and are more resistant to overcharging and deep discharge cycles. They are commonly used for energy storage systems and transportation mobility. UPS systems and back-up power supplies often use LFP battery material because they offer reliable and long-lasting power.
Addressing the Global Environmental Challenges of Battery Material Production
UniMelt – Dramatically Reducing the Environmental Impact Over Co-precipitation
Addressing environmental challenges of battery material production.
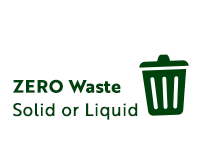
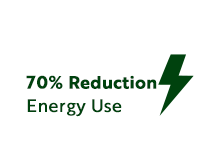
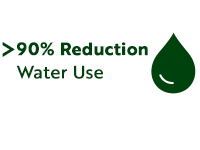
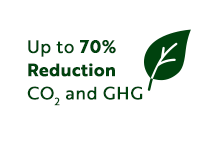
Leapfrog Technology at Significantly Lower Cost
Faster, Cleaner and at a Lower Cost
6K UniMelt® microwave plasma technology is transforming the way we produce battery material by collapsing the production process time by 95% resulting in:
To meet the demands of electrification, battery material costs must be drastically reduced, requiring production to be done differently.
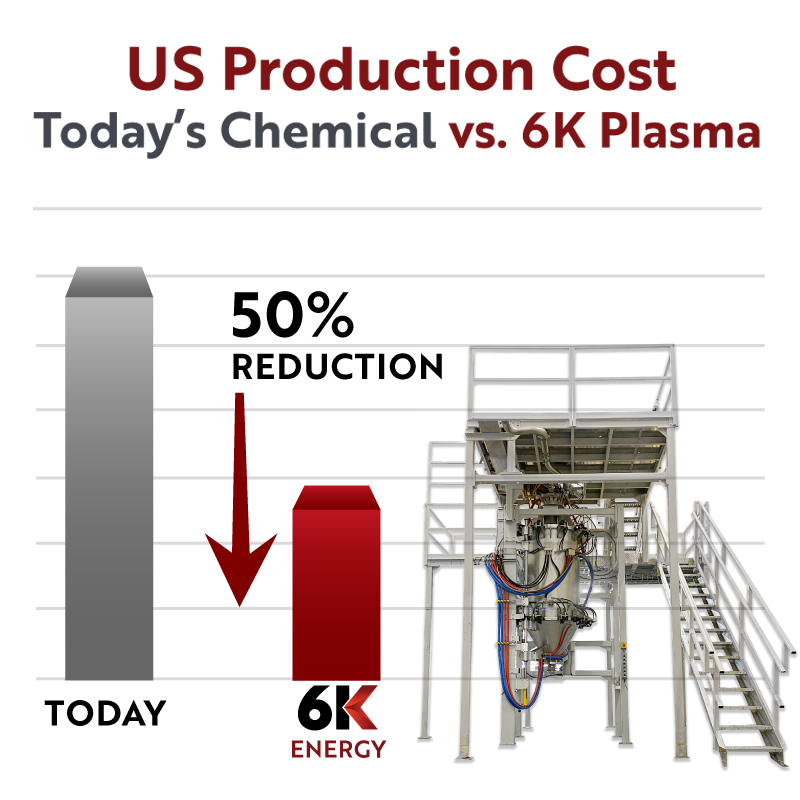
6K’s UniMelt Production Cost
With 6K’s UniMelt technology, we take a multiple-step process down to a single-step, closed-loop process, driving the overall cost of the material production down.
Domestic Battery Material Production to Ensure Supply Chain Independence
6K Energy is Establishing a Secure Supply Chain with Domestic NMC and LFP Material
Controlling domestic supply of battery material to meet local demand and government incentives.
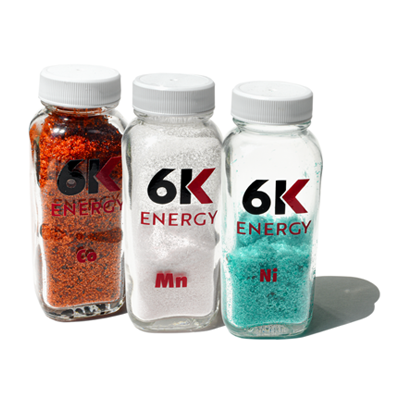
6K Energy Feedstock Made in the USA
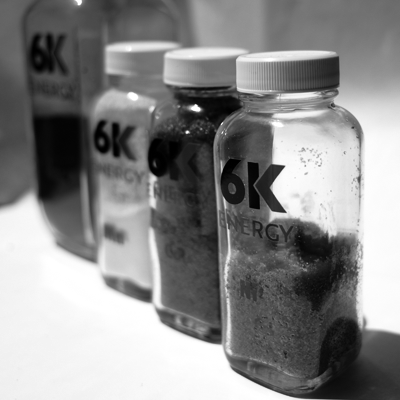
Domestic Battery Material
Full portfolio of battery material
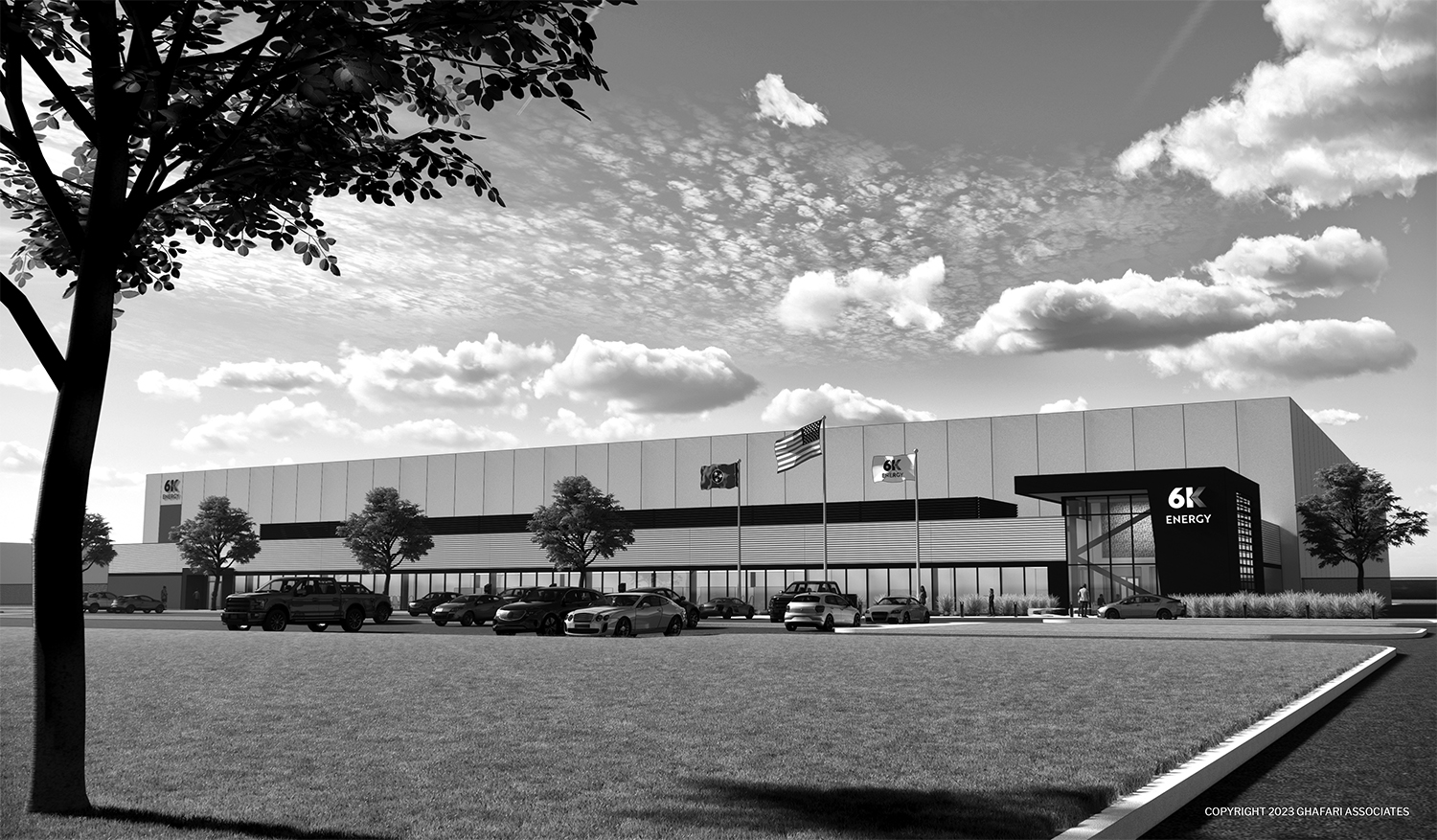
6K Energy Production Facilities
Learn about our production roadmap
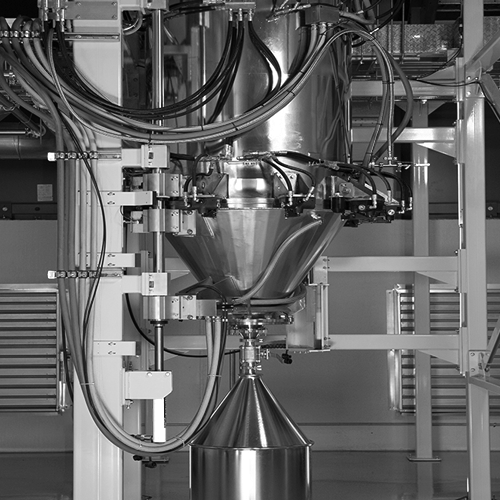
UniMelt Technology
Transforming manufacturing with microwave plasma